Precision polishing means quality finish
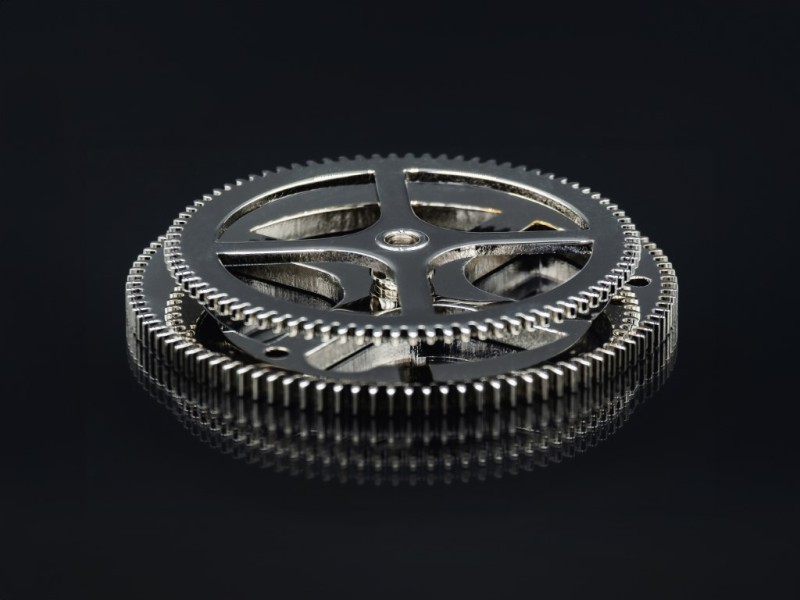
Luxury watchmaking, aeronautics and aerospace are demanding sectors. They rely on subcontractors specializing in precision polishing to achieve far superior levels of finish on their parts. Based in Franois, UND has developed specific expertise in this field.
Precision polishing, a unique expertise
Industrial sectors such as the medical, aeronautical and luxury watchmaking industries demand the highest level of finish for certain parts. The reasons for this requirement to go beyond quality standards are both functional and aesthetic. Precision polishing is needed to eliminate surface roughness, to remove the last roughness invisible to the naked eye, to make the surface perfectly smooth, uniform or shiny, and thus to obtain the desired result adapted to the constraints of a given sector.
It's a highly specific skill that combines the polisher's meticulousness with high-performance technical resources. Few polishing companies have this expertise. In Franois, in the Doubs region, at the heart of the Besançon microtechnology basin, UND has developed expertise in this field, where tolerances are in the micron range and the finish is perfect.
The company, which employs around a hundred people, initially specialized in precision screw machining, its core business. However, in response to customer demand, it has integrated high-end polishing, dedicating a workshop to it, which employs 7 people.
They mainly polish small series for the leather goods, eyewear, aeronautics and aerospace industries. Here, the demand for results is an unwavering principle. Precision is not part of the vocabulary of high-end industry players.
.
Three levels of precision polishing
UND offers its customers three levels of part finishing to suit their needs.
The first is traditional polishing. It is carried out manually by a rigorous and experienced polisher. His know-how and experience enable him to assess the level of finish of a piece reserved for the luxury market.
The second level of finishing is honing for superior quality. This is a highly precise operation. It removes any residual micro-spots and adjusts the final dimensions of a part to a tolerance in the micron range. UND uses two lapping techniques. Flat lapping, which improves surface flatness and finish, and cylindrical lapping, which improves part circularity and surface finish. Cylindrical honing is useful for ensuring a perfect fit of moving parts, particularly cylinders and bores.
The third and final finishing level is mirror polishing. To achieve this result, the polishing operation requires mastery and technical skill to mirror the surface of a part. The aim is to create smooth surfaces, free of roughness, scratches and defects.
Precision polishing is essential to achieve a perfect aesthetic result, or to ensure the function of assembled parts. Precision is a constant value in this profession, which demands a high level of mastery. Such is the case with UND in Franois, a company that has won the trust of players in the luxury goods, aeronautics and aerospace industries. UND holds the mandatory certifications that guarantee the quality of its production (ISO 9001, ISO 9100 and ISO 13485).